Am Ende ist die Trocknung immer zu klein
Das Potenzial vieler Anlagen ist noch nicht ausgeschöpft
Dem nachhaltigen Strukturwandel in der Landwirtschaft sowie dem züchterischen Fortschritt ist es zu verdanken, dass die technische und pflanzenbauliche Entwicklung als kontinuierlicher Prozess anhält. So werden von Jahr zu Jahr die Betriebsabläufe weiter optimiert. Auch hat längst eine weitere Spezialisierung der Betriebe stattgefunden. Die Fruchtfolgen auf den klassischen Marktfruchtbetrieben laufen in einer kurzen Rotation mit einem aufgeräumten Sortenspektrum.
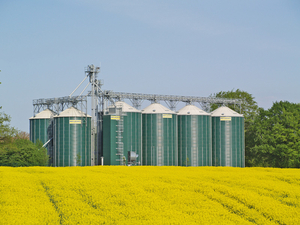
Foto: Spreu
Zu modernen Getreideanlagen gehört ein Feuchtgetreidelager
Auf vielen Betrieben ist in den letzten Jahren jedoch das Flächenwachstum über die Kapazitäten der Getreideanlage hinaus gewachsen. Da das Betriebswachstum ein sukzessiver Prozess ist, wird die Trocknung irgendwann zum Nadelöhr in der Erntekampagne. Doch bevor in neue Technik investiert wird, sollte überlegt werden, ob die technischen Möglichkeiten ausgereizt sind. Zum einen gehört zu jeder modernen Getreideanlage ein Feuchtgetreidelager, auf dem das Erntegut bis zur Verarbeitung in der Anlage zwischengelagert werden kann. Zum anderen bleiben vielerorts die Trocknungen hinter ihren Möglichkeiten bezüglich des Schwitzprozesses, dem Trocknungsziel und der technischen Konfiguration zurück.
Ein modernes Feuchtgetreidelager wird mangels Alternativen üblicherweise unter freiem Himmel errichtet. Damit dieses Zwischenlager den Erfordernissen der guten fachlichen Praxis entspricht gilt es jedoch einige Dinge zu beachten: Als Untergrund muss eine planbefestigte Fläche vorhanden sein, die einer Radlast von 8 t standhält. Diese Fläche muss ein Gefälle von mindestens 2 Prozent aufweisen, damit sich kein Wasser sammeln kann. Des Weiteren sollten diese Flächen konvex ausgeführt sein, sodass ein Einlaufen von Wasser unter das Lagergut nicht möglich ist.
Wird das Feuchtgetreidelager mit Seitenwänden eingefasst, sollten lediglich an den Längsseiten beschüttbare Wände entstehen, so dass das Fechtgetreidelager von zwei Seiten zugänglich ist. Dies verhindert tote Ecken in denen das Lagergut verderben kann. Zum Schutz vor Regen und Kontamination sollte ein Vlies Verwendung finden. Dieses ermöglicht den für den Trocknungsprozess notwendigen Schwitzprozess ohne jedoch Schwitzwasser zu bilden und verhindert das Eindringen von Regenwasser. Zum Errichten von beschüttbaren Wänden in temporären Zwischenlagern haben sich in der Praxis Betonlegosteine bewährt. Diese können nach der Erntekampagne ohne weiteres wieder demontiert werden. So kann von Jahr zu Jahr die Lagergröße variiert werden und es entstehen keine Rückzugsmöglichkeiten für Schädlinge.
Ungenutzte Potenziale bei der Durchlauftrocknung
Neben der Errichtung eines Feuchtgetreidelagers gibt es in vielen Getreideanlagen noch ungenutzte Potenziale beim Durchlauftrockner. Oft wird der Schutzprozess zu wenig ausgereizt. Die Folge ist, dass sehr heterogene Ware den Trockner passiert und eine Anpassung der Austragszeiten notwendig macht. Es liegt in der Natur der Sache, dass der Trocknungsprozess träge vonstattengeht, wodurch eine genaue Einstellung des Trockners nach der Eingangsfeuchte bei wechselnden Feuchtigkeiten nahezu unmöglich ist. Daher wird mitunter auf Unterfeuchte getrocknet, damit keine Probleme in der Lagerung entstehen.
Das Schwitzen des Getreides hat neben dem Feuchteausgleich zwischen den Körnern jedoch einen weiteren Effekt, denn während des Schwitzprozesses diffundiert die Feuchte von innen an die Kornoberfläche. Diese Oberflächenfeuchte lässt sich schneller abtrocknen als die osmotisch gebundene Feuchtigkeit im Trocknungsgut. Dieses erhöht die Passagegeschwindigkeit im Trockner um bis zu 25 Prozent. Für den Schwitzprozess gelten je nach Fruchtart unterschiedlichen Zeiten. Für Kleinsämereien wie Raps sind 6 bis 12 Stunden ausreichend. Getreide wie Gerste, Roggen und Weizen sollten 12 bis 24 Stunden schwitzen. Großsämereien wie Mais, Erbsen und Bohnen benötigen jedoch 24 bis 48 Stunden für den Wassertransport aus dem Korninneren bis zur Kornoberfläche. Der Schwitzprozess ist jedoch nicht grundsätzlich vonnöten. Bei Feuchtegehalten über 20 Prozent kann das Getreide direkt dem Trocknungsprozess zugeführt werden, da ein Schwitzprozess bei diesem Feuchtegehalt keinen positiven Effekt bringt.
Trocknungsziel oberhalb von 14,5 Prozent ansetzen
Für eine möglichst effiziente Trocknung ist eine Definition der Trocknungsziele notwendig. Ein Heruntertrocknen auf 14,5 oder gar 14 Prozent ist in den meisten Fällen unnötig, denn das Trocknungsgut verlässt den Durchlauftrockner mit 30 bis 35°C und kühlt auf dem Weg über die Förderwege um bis zu 10°K ab. Dies führt zu einem zusätzlichen Trocknungseffekt von 0,5 bis 0,75 Prozentpunkte. Somit sollte das Trocknungsziel oberhalb von 14,5 Prozent angesetzt sein. Das spart zum einen Heizöl und Strom und zum anderen erhöht es die Passagegeschwindigkeit im Trockner. Denn pro Prozentpunkt entstehen Kosten in Höhe von etwa 1 Euro/t. Des Weiteren sollten Trocknungsvorgänge, die mehr als 4 Prozent Feuchteentzug vorsehen, geteilt werden, da sonst die Passagegeschwindigkeit im Durchlauftrockner unverhältnismäßig beeinträchtigt wird. Der dann neuerlich einsetzende Schwitzprozess sorgt wiederum dafür, dass das osmotisch gebundene Wasser im Korn nach außen an die Kornoberfläche diffundieren kann. Für die Praxis bedeutet das, dass bei Kornfeuchten über 19 Prozent zweimal getrocknet werden sollte.
Reserven bei der Einstellung des Durchlauftrockners
Die Größten Reserven in bestehenden Getreideanlagen bestehen jedoch vielerorts in der Konfiguration des Durchlauftrockners. Die üblichen Steuerungsvorgänge werden durch den Feuchtegehalt des bereits ausgetragenen Trocknungsguts bestimmt, indem die Passagegeschwindigkeit mittels der Austragungseinheit angepasst wird. Dies lässt jedoch nur den Schluss darauf zu, dass der Trocknungsprozess zum Zeitpunkt, indem sich das Trocknungsgut noch im Trockner befunden hat optimal oder aber nicht optimal war. Dadurch wird der Steuerungsvorgang eher zu einem Ratespiel als zu einer echten Prozesssteuerung. Dies führt zwangsläufig dazu, dass kaum ein Trockner im tatsächlichen Betriebspunkt läuft. Des Weiteren besteht eine Unkenntnis darüber, welche Luftmenge aktuell vorhanden beziehungsweiseoptimal für den Trocknungsvorgang ist. An vielen Trocknern befinden sich zwar Regelungsmöglichkeiten für die Luftführung, wie eine Drosselklappe, allerdings gibt es keinen Monitor, welcher die aktuelle Luftmenge anzeigt.
Messen im Abluftschacht
Bei vielen Trocknern wurde schon während des Aufbaus keine Werkseinstellung vorgenommen, weil es oft einfach vergessen wurde. Somit sind in manchen Trockner, vorzugsweise jene, in denen die Trocknungstemperatur öfter das Sicherheitsthermostat auslöst, die Luftraten zu gering und in den Trocknern, die die Trocknungstemperatur nicht erreichen, zu hoch. Eine professionelle Kalibrierung der Prozessluft kann hier Abhilfe schaffen und helfen, bares Geld zu sparen. Darüber hinaus ist es ratsam, die Temperatur sowie die relative Luftfeuchtigkeit im Abluftschacht zu ermitteln. Dies hat den großen Vorteil, dass ein Indikator zur Verfügung steht, der die Veränderung im Trocknungsprozess unmittelbar anzeigen kann. So erhöht sich beispielsweise die relative Luftfeuchtigkeit bei gleichzeitiger Absenkung der Temperatur, wenn sich der Feuchtegehalt des eingehenden Trocknungsgutes erhöht. Daraufhin kann dann adäquat reagiert werden, indem die Austragung verlangsamt wird.
Diese Regelungsmechanismen funktionieren nur in engen Grenzen bereits vollautomatisch und werden auch von einigen Trocknerherstellern schon seit längerem angeboten. Eine alternative Lösung kann im ersten Schritt eine günstige Wetterstation mit Außensensor über die Parameter im Abluftschacht informieren. Insgesamt bleibt festzustellen, dass das Potenzial vieler Trocknungsanlagen noch nicht ausgeschöpft ist. Es ist deshalb ratsam, diese Reserven aufzudecken und auszunutzen. Ist dies bereits geschehen, ist über eine Investition in die Nachernteaufbereitung nachzudenken.
Albert Spreu, Rationalisierungs-Kuratorium für Landwirtschaft (RKL), Rendsburg – LW 20/2016